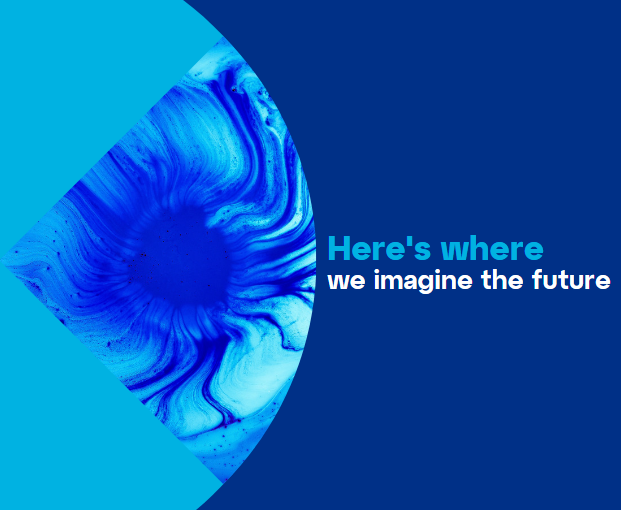
As the world’s demand for digital technologies grows, new production facilities need to be brought online quickly. As the nature of these technologies changes, so too do the facilities in which they are developed and produced.
Drivers and trends
In the decade since 2011, the world’s top R&D investors increased investment by 68% and employment by 16%. But looking forward, how can the semiconductor industry invest in an uncertain future?
Five current trends offer a glimpse of possible futures:
- Technologies will continue to miniaturise and amalgamate
- High-tech will increasingly rely on, and be driven by contamination control
- Automation and smart systems are needed to support contamination control
- Robotics will redefine the nature of safety in the production facility
In addition to these are the realities of rising costs, increasingly limited availability of scarce gases and rare metals, and the need to manage the risk of investing in production facilities that are continuously subject to changing production processes.
Growing demand for strategic approach
Deerns is where collaboration, innovation and expertise come together to address these challenges. Our process involves a holistic approach where we identify the driving forces and critical uncertainties of each project, develop plausible scenarios, and discuss the implications and ways forward with clients to help them make informed decisions.
Because technologies are constantly changing and imposing different conditions for buildings, we carefully assess what R&D teams are working on as they devise the products that will be produced in the future. Technologies are usually invented and developed at universities and/or research institutes before moving into the production environment. So, we work with these R&D entities as well as our production clients for a clear understanding on the necessary evolution of production. This helps us to ask the right questions and challenge assumptions with a view to offering solutions.
" We are engaging with major clients in scenario planning up to 2035.
This way of thinking is fundamental to our strategy with many of our clients, and we notice a growing need for this type of strategic consultancy to deal with aspects of cost efficiencies, design uncertainties, lifecycle planning and sustainability conditions.
Fit for the long run
Tomorrow’s technologies will be different from the products we use today, and this impacts on buildings and the environment. The worst risk is for a building to not be aligned with current and future production processes. So fit for use is the ultimate risk mitigation.
Some criteria to consider are, for example:
- Requirements imposed by current and future production processes
- Functional set-up and (future) size of the building(s)
- Primary utilities (power, heating and cooling)
- Chemicals/gases and whether they need to be reused/recycled
- Emissions resulting from processes.
The sooner these factors are known, the better. This can be challenging. Typical R&D programmes last for three to four years, yet a R&D building must operate for 20 to 30 years. Even if you build something that is fully aligned with a product in progress, it will only be aligned for a few years.
The facilities must work for next generation as well as current technologies. And it is sometimes also necessary to plan for repurposing the building down the line. It’s really about considering the entire lifecycle of the facility. This requires overall strategic thinking which includes catering for a company’s product programming spectrum and the possibilities and cost of adapting the building after a couple of years.
Here’s where we see Challenges as Opportunities
As soon as the need for a new production facility has been identified, companies should start to think about the requirements, the risks and cost implications. This discussion should happen right at the outset, well before the design gets underway, and will help to determine where the facility is located as well as offer guidance to the architect. This is the type of strategic involvement that our clients expect from us – so much so that we are engaging with major clients in scenario planning up to 2035.
This approach helps to address both internal and external complexities. One of the big challenges we are seeing in the Netherlands, for example, is that facility owners need to accommodate more functionality, but space for new developments is limited because land is so expensive. Accordingly, there is a move towards facilities becoming more vertical, which significantly affects how the design and logistics will work and adds to the complexity of constantly evolving technologies, increasingly stringent environmental regulations, and legacy systems that must be replaced.
Deerns’ multidisciplinary team is able to take all these criteria into consideration, guide the architectural design process, and come up with integrated engineering solutions to help clients overcome these challenges.
And, because we work on a range of different projects with clients in diverse sectors, we are able to take lessons learned from past projects and apply them to new projects. A challenge for one client becomes an easy solution for another. Our value lies in being able to ask the right questions and apply innovative thinking in an appropriate way.
" The end game is facilities that are more connected, interchangeable and adaptive – factories that are ready for the future.