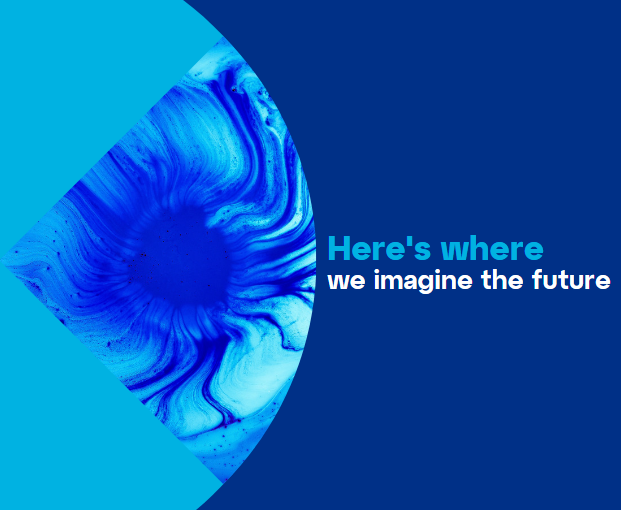
Deerns takes the whole life carbon approach to the next level on a public building constructed entirely from recycling materials from a bank.
Whole Life Carbon provides a framework for achieving decarbonisation across the construction sector beyond cost to environmental impact. It’s a point the Dutch government is taking to the next level with the mounting pressure to build sustainably and circularly, partly due to European laws and regulations. This approach was evident in the pilot project Kantoor Vol Afval (Office Full of Waste), set up as a test case for the renovation of the former Valkenburg Air Base, by using (almost) exclusively recycled materials. On the back of winning a tender, Deerns and the Government Real Estate Agency (RVB) joined forces for this innovative project.
As a member of the Circularity Programme of of the Dutch Green Building Council (DGBC), Deerns actively contributes to ideas on for circular construction. We centre this on three core principles:
- Careful handling of materials to avoid depleting our resources
- Minimising environmental impact by choosing materials with low carbon emissions
- Making buildings adaptable so that they can be used for longer periods of time
Decarbonisation with Whole Life Carbon
How do you design a building that meets the Paris-Proof standards in terms of environmental impact? The answer seems obvious: by measuring the building’s carbon emissions during use. Yet this gives a limited picture. For example, triple glazing has a low footprint due to its good insulation, but its production causes excessive CO₂ emissions.
To get a complete picture, Whole Life Carbon calculates the material’s emissions over the entire life cycle. This comprehensive approach includes the following factors:
Embodied carbon: The amount of CO₂ and other greenhouse gases emitted during the extraction of raw materials, production, transport, assembly, maintenance and demolition or reuse of building materials.
Operational emissions: the CO₂ emissions during the use of the building, e.g. from heating, cooling, lighting and other building-related activities.
The Whole Life Carbon approach allows us to compare building materials not only on cost, but also on environmental impact. This leads to more informed decisions at the design stage. Moreover, it encourages supplier innovations to reduce the embodied carbon of materials.
" In addition to the ‘energy transition’, we have now entered a ‘materials transition’, which involves thinking more consciously about the origin of materials.
Deerns was one of the first Whole Life Carbon ambassadors and a pioneer in creating awareness in this area. Moreover, Deerns applies this methodology in several projects. Thanks to the cross-pollination with the DGBC, we stay abreast of the latest trends and developments in circular building.
Bank Waste to New Office: Test case for circularity
The old ABN AMRO office in Amsterdam was the donor building for the renovation of the former Valkenburg Air Base. With matching functions, a lot of material could be repurposed immediately. The challenge was to create a high-quality office so a lot of attention was paid to the performance requirements and quality of the reused materials.
This immediately brought a major challenge. Both architectural and installation materials need to standards and regulations, for example acoustics and fire safety which are usually set for new materials. For reused materials this information is either not readily available or does not meet current requirements. \This meant we had to take on additional testing. By comparing several options side by side, performing simulations and staying in dialogue with the RVB, we managed to make the best choices. This involved concessions, such as accepting that slightly higher noise levels in some places or buying new data cables.
Now that completion is behind us, both Deerns and RVB consider this as a pace setter for the urgent need to turn down the volume on carbon emissions. Despite the challenges, we have shown that it is possible to design a high-quality office building with largely circular materials. This learning process will contribute positively to future construction projects.
Regenerative construction is the future
At Deerns, circular building and Whole Life Carbon are more than separate concepts.
" We apply Whole Life Carbon proactively in our projects with an eye on our ultimate prize: regenerative building.
Designing buildings that add value, close chains, restore rather than disrupt and interchange with the environment. We work towards a future where we build not only for people, but also for the environment. And we are always willing to go the extra mile for this.