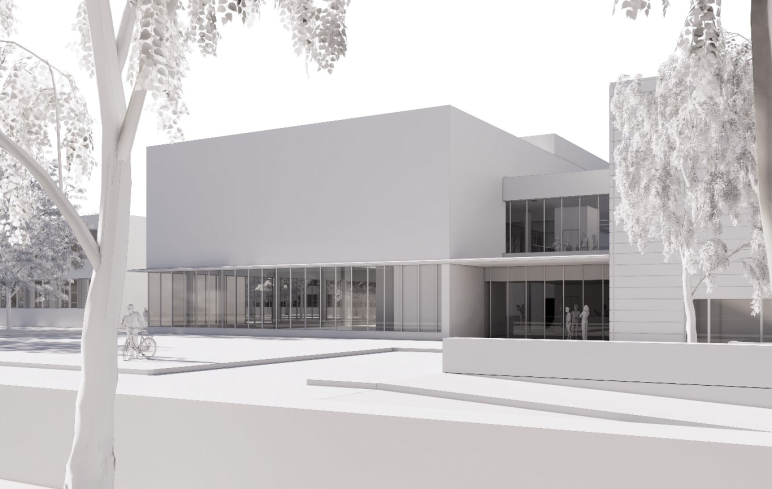
Deerns design of state-of-the-art cleanroom for the Technical University of Denmark is greatly enhancing nanofabrication R&D capabilities.
Deerns’ multi-disciplinary expertise and experience in the Life Sciences and Electronics sectors have enabled end-to-end support for the Technical University of Denmark (DTU), a prestigious institution known for its excellence in engineering and technology research. The university has commissioned the construction of a new state-of-the-art cleanroom for DTU Nanolab, the National Centre for Nanofabrication and Characterisation in Denmark. This new facility, adjacent to an existing cleanroom, will support research into next-generation microchips at the nanoscale level.
DTU Nanolab is an open-access research infrastructure facility that serves both academic and commercial entities. It houses advanced processing equipment within its 1,350m² cleanroom facilities and features a suite of nine advanced electron microscopes. The new cleanroom, covering approximately 650m² with an additional 250m² in a future phase, will further enhance the research capabilities of DTU Nanolab, supporting the European community’s efforts in the electronics market and semiconductor industry.
Overcoming Design Challenges on a Tight Schedule
For the past 18 months, Deerns has been assisting with user requirements and design criteria.
The collaboration between Danish and Dutch teams exemplifies the synergy between the two countries, leveraging their strengths to achieve a common goal,” says Eric Stuiver, Sector Director, Electronics at Deerns. “This shared approach is based on efficiency and similar work cultures.
This collaborative approach, Deerns’ pool of expertise across engineering disciplines, has been highly effective, contributing significantly to the project’s success. The project kicked off in November 2023.
Deerns was assigned to the design team, completing the concept design in April and moving into the basic design phase that runs until August; followed by a review process before the tender phase. The project is set for completion in 2026. The timeline is tight, with excavation occurring in parallel to the tender phase to ensure that deadlines are met.
The most significant design challenges that the team faces are:
- The fast-moving cleanroom industry demands flexibility and future-proofing, ensuring that the facility remains relevant for the next 10-15 years as technology advances. Smaller chips require larger, more energy-intensive facilities. The design must therefore balance energy efficiency requirements with market demands, while working within the client’s budget.
- Research at the nanometre level is highly sensitive to vibration and electromagnetic interference. Roads and traffic adjacent to the site, as well as the construction of a nearby tram rail pose significant challenges. Vibration mitigation and electromagnetic shielding are crucial to ensure the integrity of the research.
- Minimising contamination from air particles and other sources is always a critical challenge in cleanroom design. This project is particularly challenging because the route for transporting chemicals and gases between the new cleanroom and the logistics building passes through the adjacent existing cleanroom.
- The new building will be constructed on top of existing drainage and stormwater lines, and existing service tunnels will need to be adjusted. The proximity to the existing operational Nanolab, itself sensitive to vibration and electromagnetic interference, adds to the complexity. The project’s success hinges on maintaining the operational integrity of the adjacent facilities while constructing the new cleanroom.
Existing transformer rooms that supply surrounding buildings will need to be moved during construction and then relocated into the new building. This involves careful planning to ensure uninterrupted power supply to the existing facilities during the transition.
Custom Installations
Deerns is responsible for all installations, including:
- Chemical and gas systems
- Heating, ventilation, and air conditioning (HVAC)
- Plumbing
- Water drainage
- Transport installations
- Fire safety
- Electrical systems
- Waste collection of chemicals and gases
The cleanroom systems will reclaim heat to reuse in air handling units and recirculate process cooling water on campus. The client is targeting DGNB certification from the German Sustainable Building Council. This rating assesses buildings based on socio-cultural and functional quality, environmental quality, economic quality, technical quality, and process quality.
Here’s where we strengthen ties through shared Work Cultures
Deerns’ team includes up to twenty experts from various disciplines, ensuring a tailored solution that meets the client’s needs. Collaborating closely with Danish consultants ensures that the design incorporates local regulations and standards, enhancing the project’s feasibility and compliance. Leveraging this local expertise is vital for addressing the site-specific challenges unique to this project.