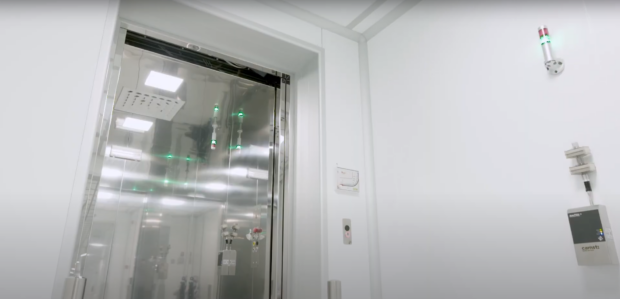
Fresenius Medical Care wilde de capaciteit van de bestaande cleanroom uitbreiden om meer levensreddende dialyseapparatuur te kunnen produceren. De capaciteit kon alleen worden uitgebreid door een tweede cleanroom te creëren op een andere verdieping van het gebouw. Deerns ontwierp voor Fresenius Medical Care daarom een clean lift-systeem dat de bestaande cleanroom naadloos verbindt met de nieuwe cleanroom. Zo ontstond een gestroomlijnd productieproces, waarbij het risico op contaminatie tot een minimum is beperkt om de kwaliteit van de apparatuur te borgen.
Levensreddende dialyseapparatuur
Met 44 productiecentra wereldwijd is Fresenius Medical Care de belangrijkste leverancier van dialyseapparatuur en -toebehoren in de wereld. Naast de verschillende productiecentra heeft Fresenius een wereldwijd netwerk met 4.151 dialysecentra opgebouwd, waar ongeveer 345.000 patiënten worden behandeld. Wereldwijd ondergaan circa 3,7 miljoen mensen regelmatig een dialysebehandeling, een behandeling die onmisbaar is voor patiënten met nierfalen.
Extra geautomatiseerde productiecapaciteit
Fresenius zet in op samenwerking, betrouwbaarheid, kwaliteit en proactiviteit en wilde mede daarom de bestaande cleanroom op de eerste verdieping van het productiecentrum in Palazzo Pignano (Italië) uitbreiden. Wanneer er, zoals bij Fresnesius, grote hoeveelheden producten worden geproduceerd wordt een extra cleanroom bij voorkeur op dezelfde verdieping gerealiseerd vanwege de strenge eisen die aan het productieproces worden gesteld. Zo is het belangrijk dat zwevende deeltjes en biologische verontreinigingen worden gecontroleerd en gereguleerd om fouten te voorkomen, de proceskwaliteit te waarborgen en het personeel en milieu te beschermen. Bij Fresenius kon een tweede cleanroom uitsluitend op de begane grond worden gerealiseerd.
In de bestaande cleanroom op de eerste verdieping wordt een halffabricaat geproduceerd, dat vervolgens verder wordt verwerkt door vier halfautomatische machines. Door ruimtegebrek in de moesten deze machines in een nieuwe cleanroom op de begane grond worden geïnstalleerd. Om een continu productieproces te garanderen, ging Fresenius op zoek naar een oplossing waarmee de bestaande cleanroom op de eerste verdieping naadloos en met een minimaal risico op contaminatie met de nieuwe cleanroom op de begane grond kon worden verbonden. Dit vereiste een oplossing voor de schone logistiek tussen de twee verdiepingen die een strikte controle van verontreinigingen en thermo-hygrometrische parameters kon garanderen.
Vertrouwde adviseur
Na het ontwerp van de eerste cleanroom in 2017 heeft Deerns Italia verschillende andere projecten uitgevoerd voor het productiecentrum van Fresenius Medical Care in Italië. Als vertrouwde adviseur werd Deerns gevraagd om een oplossing te ontwikkelen voor de gewenste uitbreiding van de cleanroom. Deerns was daarbij verantwoordelijk voor het ontwerp, de aanvraag van de benodigde vergunningen, het toezicht op de uitvoering, het testen, de inbedrijfstelling en de validatie van een clean lift-systeem voor zowel medewerkers als producten. De cleanrooms en het bijbehorende liftsysteem moesten voldoen aan ISO-richtlijnen voor ‘operationele’ cleanrooms.
Geavanceerd clean lift-systeem
Het clean lift-systeem dat Deerns heeft ontwikkeld, verbindt de bestaande cleanroom met de nieuwe cleanroom, zodat producten direct naar de volgende fase van het productieproces kunnen worden vervoerd en een continu productieproces is gegarandeerd. Daarnaast heeft Deerns verschillende complexe installaties ontworpen om aan de eisen voor temperatuur en relatieve luchtvochtigheid voor ISO klasse 8-cleanrooms te voldoen. Ook was Deerns verantwoordelijk voor de energievoorziening van de nieuwe cleanroom.
Naadloze verbinding
Het unieke clean lift-systeem van Deerns bestaat uit een liftcabine, een liftschacht en op beide verdiepingen twee luchtsluizen naast elkaar. Dankzij dit ontwerp kunnen de halffabricaten direct naar de cleanroom op de begane grond worden vervoerd, zonder de gecontroleerde omgeving te verlaten. De luchtsluizen van beide cleanrooms zijn bovendien voorzien van een PAL (Personnel Airlock) en MAL (Material Airlock). De gebruiksvriendelijke interface voor de regel- en bewakingssystemen zorgt er tot slot voor dat medewerkers – en in de toekomst AGV’s – de lift veilig kunnen gebruiken zonder risico op contaminatie van de producten.
Drie ventilatiesystemen voor één lift
Om het vereiste reinheidsniveau in de liftcabine, de liftschacht en de twee luchtsluizen te garanderen, worden er gescheiden ventilatiesystemen gebruikt. De liftcabine en de twee luchtsluizen zijn voorzien van een speciale luchtbehandelingskast en een ventilatiesysteem. Deze zorgen ervoor dat het vereiste reinheidsniveau voor ISO-klasse 8-cleanrooms wordt gewaarborgd. Het ventilatiesysteem van de liftcabine bestaat uit een aparte filtereenheid met een HEPA H14-filter. Ook de liftschacht is voorzien van een eigen ventilatiesysteem.
De verschillende ventilatiesystemen worden aangestuurd door een PLC-regelsysteem dat is gekoppeld aan een speciaal monitoringsysteem. Dit monitoringsysteem, dat gebruikmaakt van drie optische deeltjestellers en sensoren voor temperatuur, relatieve vochtigheid en drukverschil, bewaakt continu de verschillende parameters in de liftcabine, de liftschacht en de twee luchtsluizen. Het vereiste reinheidsniveau wordt geborgd door contaminatie nauwkeurig te controleren en reguleren en tegelijkertijd redundantie (niveau n+2) toe te passen in het ontwerp.
Materiaalkeuze
Bij de keuze van de materialen heeft Deerns vooral gelet op eigenschappen zoals reinigbaarheid, retentie en desintegratie. De liftcabine is gemaakt van een combinatie van roestvast staal en glas en is voorzien van schuifdeuren. Voor de liftschacht is beton gebruikt dat is voorzien van een speciale epoxyhars. Voor de aandrijving van de lift wordt een hydraulisch systeem gebruikt met speciaal ontworpen zuigers en veiligheidskleppen, waardoor slechts een minimale hoeveelheid deeltjes vrijkomt bij de bewegende onderdelen.
Het gehele project, van het ontwerp en de aanvraag van de vergunningen tot de uitvoering door de aannemer, werd in slechts 3 maanden uitgevoerd.
" Wij danken ons succes aan de inzet, betrokkenheid en efficiëntie van onze medewerkers en partners bij dit project.